Solvents for Printing Ink on PE Film: Roles, Applications and Usage Tips
30/06/2025
|
Industry news
PE ink solvent is a specialized chemical used in gravure and screen printing, playing a crucial role in achieving sharp, well-adhered, and durable print quality. So, what exactly is PE ink solvent? What are its characteristics, applications, and the pros and cons of commonly used polyethylene solvents today? Let’s explore with K-Chem in the article below.
What Is PE Ink Solvent?
PE ink solvent refers to chemicals used to dilute ink printed on polyethylene (PE) surfaces, helping adjust viscosity, improve adhesion, and enhance print quality. These are specialized solvents designed for printing technologies, especially gravure and screen printing on plastic surfaces like PE, PP, and OPP.
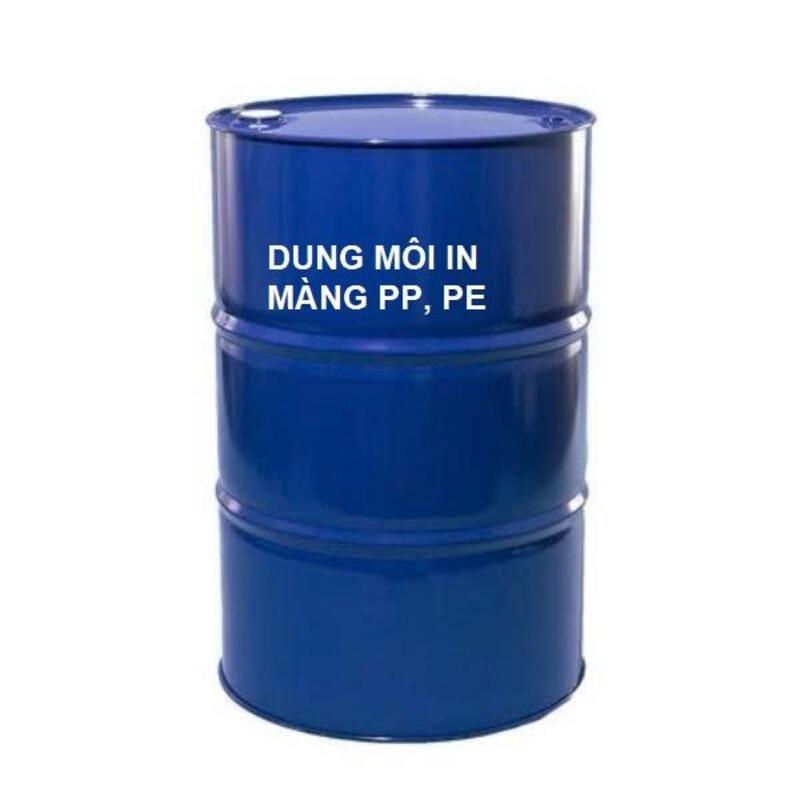
Key Functions of PE Ink Solvent
- Dissolving ink components: The solvent plays a crucial role in dissolving the components in ink, helping create a uniform mixture that is easy to use and prevents clumping during printing.
- Anti-clogging and drying control: Solvents slow down evaporation, preventing the ink from drying too quickly on the printing plate, thus avoiding hardening and screen clogging during screen printing on materials like PP and PE.
- Achieving optimal fluidity for uniform coating: Solvents help adjust ink viscosity to reach optimal fluidity, allowing even coverage on product surfaces. This results in uniform coloration, high gloss, and improved colorfastness during long-term storage.
Top 6 Solvents for Gravure Ink on PE Film
Depending on the printing technology (gravure or flexographic), technicians must choose the right solvent for PE film inks. The solvent must effectively dissolve ink, enhance adhesion, match the drying speed of the printer, and be compatible with the non-absorbent nature of PE film. Below are common types of solvents and their features, based on compiled information:
Gravure printing uses low-viscosity ink (around 0.1 Pa.s), primarily dried by solvent evaporation. Common solvents include:
Ethanol
- Characteristics: A widely used solvent, volatile, and more environmentally friendly than hydrocarbon-based solvents.
- Application: Commonly used to dilute ink to improve adhesion on PE film.
- Advantages: Good solubility, less toxic compared to many other organic solvents.
- Disadvantages: Highly flammable; must be used in well-ventilated areas away from heat sources.
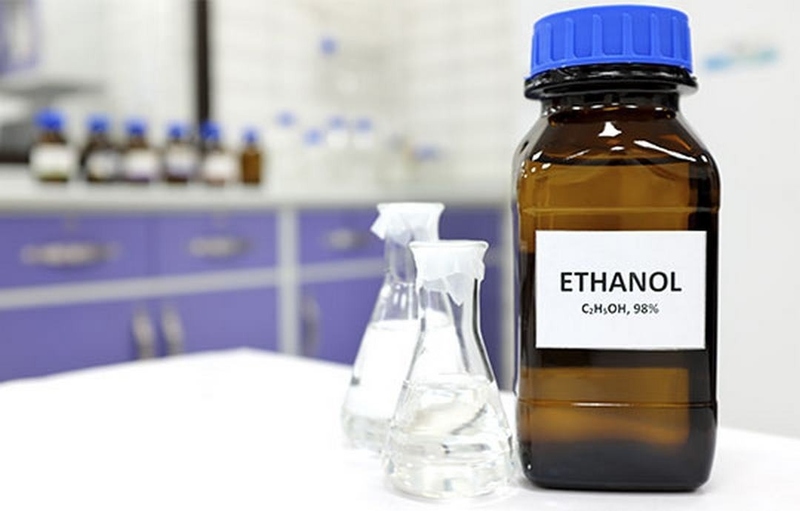
N-Propanol
- Characteristics: Slower evaporation rate than ethanol, allowing better control of ink viscosity and drying, suitable for high-speed printing.
- Application: Used to formulate inks with appropriate viscosity for gravure printing.
- Advantages: Excellent solubility, safer than solvents like toluene, balanced evaporation for high-speed printing.
- Disadvantages: Expensive and flammable.
N-Propyl Acetate
- Characteristics: Enhances solubility and improves adhesion on PE surfaces while maintaining color stability.
- Application: Used in ink formulation for gravure printing to enhance adhesion on PE film.
- Advantages: Good solubility, balanced evaporation rate.
- Disadvantages: High cost.
Toluene
- Characteristics: Highly effective in dissolving resin and ink but toxic, raising environmental and health concerns. Many manufacturers are moving toward toluene-free inks.
- Application: Common in gravure ink systems.
- Advantages: Fast evaporation, enabling quick drying of ink on print surfaces.
- Disadvantages: Highly toxic; must be used in ventilated environments with protective equipment like gloves and masks.
Diethylene Glycol (DEG)
- Characteristics: High solubility and boiling point, low volatility; often used to improve ink adhesion and stability.
- Application: Suitable for printing on PE film and other plastic surfaces.
- Advantages: Excellent solubility, low volatility.
- Disadvantages: Toxic; requires protective equipment and proper ventilation during use.

Isopropanol
- Characteristics: Used to adjust ink viscosity and drying speed, especially in ink systems requiring high adhesion on PE film.
- Application: Common in ink formulation or as a cleaning agent for printing equipment.
- Advantages: Fast evaporation, good solubility.
- Disadvantages: Flammable and may cause irritation upon direct contact with skin or eyes.
General Characteristics
- Solvents for gravure printing require high diffusivity to ensure good ink adhesion on non-absorbent PE surfaces.
- Evaporation rate must align with the printer speed (typically 200 m/min or higher) to avoid smudging or image distortion.
- Solvents like ethanol and n-propanol are often preferred due to lower toxicity and better compliance with environmental standards.
TOP 5 Solvents for Flexographic Ink on PE Film
Flexographic printing commonly uses either water-based or solvent-based inks, depending on the product requirements and the specifications of the printing machine. Common solvents include:
Water (H₂O)
- Characteristics: Mainly used for water-based flexographic inks, water is safe and environmentally friendly. To enhance adhesion on PE film, a small amount of organic solvent such as ethanol or isopropanol is often added. The drying mechanism is primarily absorption (70%) and evaporation (30%).
- Application: Used as the main solvent for flexographic inks on PE film.
- Advantages: Safe, non-toxic, eco-friendly, low-cost, and easy to obtain.
- Disadvantages: Poor adhesion and slower drying time compared to organic solvent-based inks.
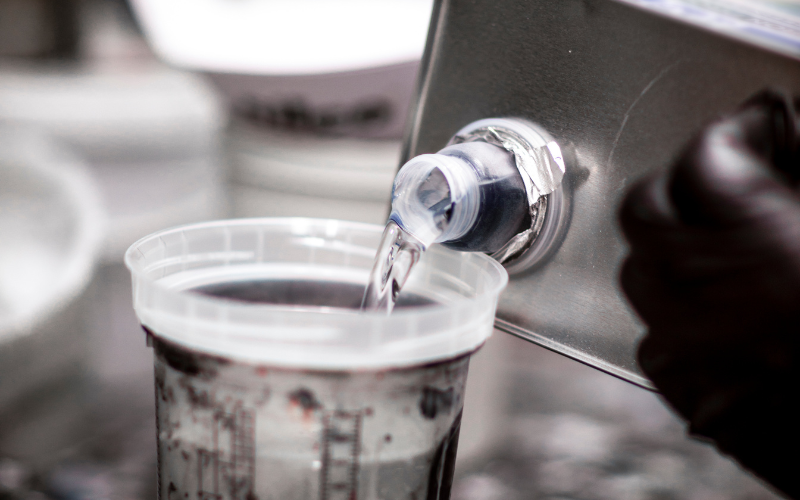
Ethanol
Similar to gravure printing, ethanol is the primary solvent in solvent-based flexographic inks. It enhances ink adhesion to PE film and enables fast drying.
Isopropanol
Used to adjust viscosity and improve adhesion on plastic surfaces. Often combined with ethanol for optimal performance.
N-Propanol
Suitable for flexographic ink systems requiring slower drying times to prevent ink smearing on PE film surfaces.
Ethyl Acetate
- Characteristics: Enhances resin solubility and improves adhesion.
- Application: Commonly used in solvent-based flexographic inks.
- Advantages: Good solubility and relatively safe for users.
- Disadvantages: High volatility.
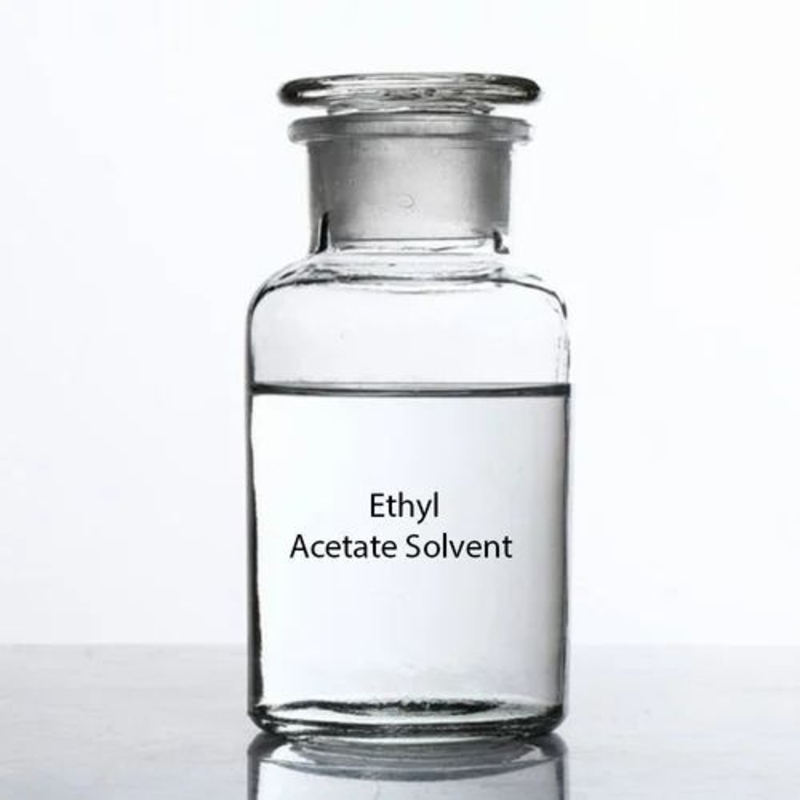
Technical Guidelines for Mixing Solvents with PE Inks
General Instructions for Mixing Solvents
- Accurate Measurement: Use a measuring cup or digital scale to ensure correct ratios.
- Stir Well: Mix solvent and ink using a low-speed agitator to avoid foaming.
- Check Viscosity: Use a Zahn cup (#2 for gravure, #3 for flexo) to measure post-mix viscosity.
- Trial Run: Test print on corona-treated PE film and evaluate adhesion (tape test), color quality, and drying speed.
- Environmental Conditions: Temperature and humidity affect evaporation rate. Recommended conditions are 20 – 25°C and 50 – 60% humidity.
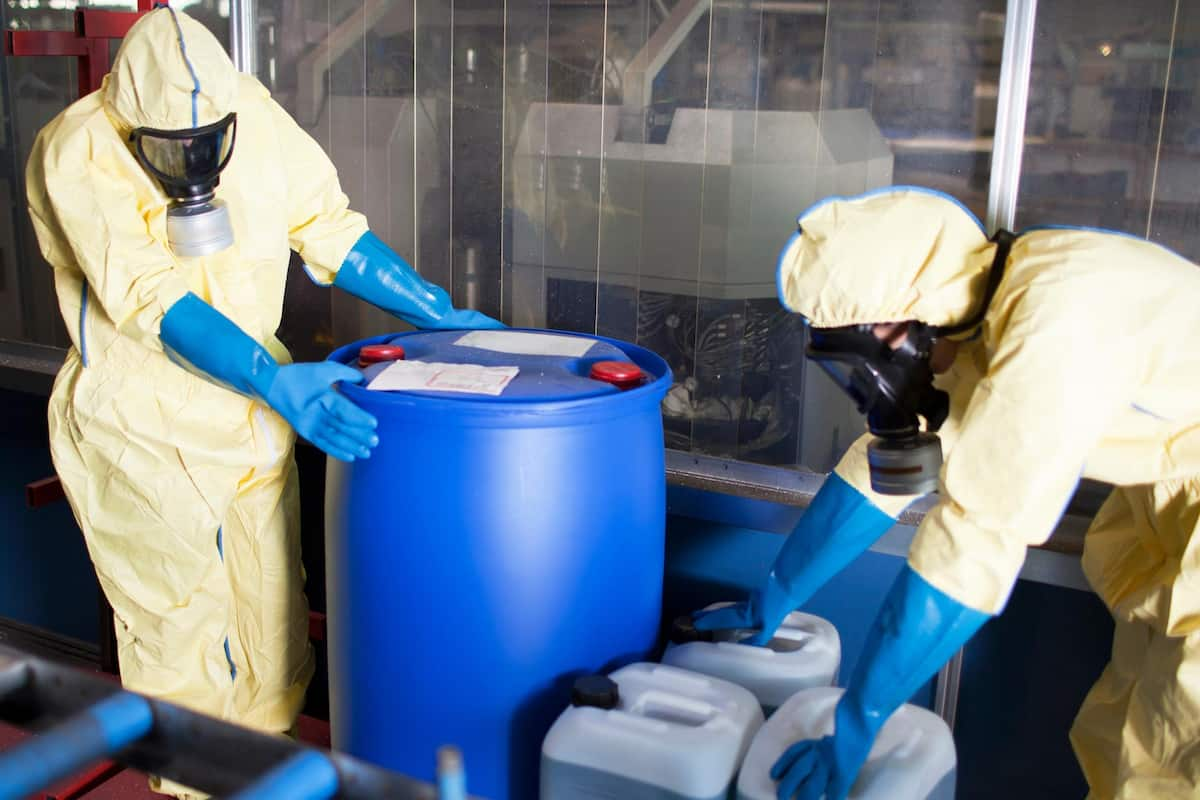
Gravure Printing on PE Film
Gravure printing uses low-viscosity, solvent-based inks that require fast-evaporating solvents to match high-speed printing and drying systems.
Formula 1: General Ink for PE Packaging (Labels, Food Bags)
- Toluene: 70%
- Ethyl Acetate (EA): 20%
- N-Propanol: 10%
- Target Viscosity: 10 – 14 seconds (Zahn cup #2 at 25°C)
- Application: Suitable for corona-treated PE film; ensures strong adhesion and fast drying.
Formula 2: High Gloss Ink (Premium Packaging)
- Toluene: 60%
- Ethyl Acetate (EA): 25%
- Xylene: 15%
- Target Viscosity: 12 – 15 seconds (Zahn cup #2)
- Application: Ideal for PE, OPP, or PET films requiring sharp print and abrasion resistance.
Formula 3: Color-Stable Ink (Large-Volume Printing)
- Toluene: 65%
- Ethyl Acetate (EA): 20%
- Diethylene Glycol (DEG): 15%
- Target Viscosity: 11 – 14 seconds (Zahn cup #2)
- Application: Suitable for continuous printing where consistent color is critical on PE film.
Notes
- Viscosity Adjustment: If ink is too thick, gradually add Toluene or EA (5% per adjustment). If too thin, reduce solvent or add more ink.
- Adhesion Test: Use tape to check ink adhesion on PE film after printing.
- Safety: Toluene and Xylene are highly flammable; ensure proper ventilation and wear protective gear.
Notes on Storage and Usage of PE Ink Solvent
- Prioritize using solvents from reputable brands to ensure print quality and safety during use.
- Do not excessively dilute the ink, as this can reduce adhesion and sharpness of the print.
- Store the solvent in a dry, cool, and well-ventilated place. Avoid direct sunlight, heat sources, or areas with fire/explosion hazards.
- Minimize direct contact with skin and eyes. In case of contact, rinse immediately with clean water and seek medical attention if irritation occurs.
- During use, wear gloves, a mask, and work in a well-ventilated area to ensure health and safety.
- Choosing a suitable PE ink solvent not only improves print quality and adhesion but also optimizes costs.
Contact K-Chem today – a trusted provider of customized PE ink solvent formulations. Leave your information or receive free consultation from our experienced experts via the contact details below:
K-CHEM VIETNAM CO., LTD
- Address: N6B Road, Lot F, Phu Chanh 1 Industrial Cluster, Phu Chanh Ward, Tan Uyen City, Binh Duong Province, Vietnam
- Tel: +84 274 362 0218
- Email: info@k-chem.vn