Guideline for Ink Thinners: Selection, Use, and Best Practices
16/05/2025
|
Industry news
Ink thinners are essential additives used to adjust the viscosity and flow characteristics of inks, ensuring they perform optimally during the printing process. Whether for offset, flexographic, gravure, or screen printing, ink thinners are crucial for achieving the desired consistency, drying time, and print quality. This guideline covers the various types of ink thinners, their functions, and practical considerations to help you make informed decisions for your printing needs.
What is Ink Thinner?
An ink thinner is a solvent or mixture of solvents added to ink formulations to reduce the ink’s viscosity, adjust the evaporation rate. The purpose of an ink thinner is to make the ink more suitable for the specific printing process, substrate, and environmental conditions, ensuring smooth application and excellent print quality.
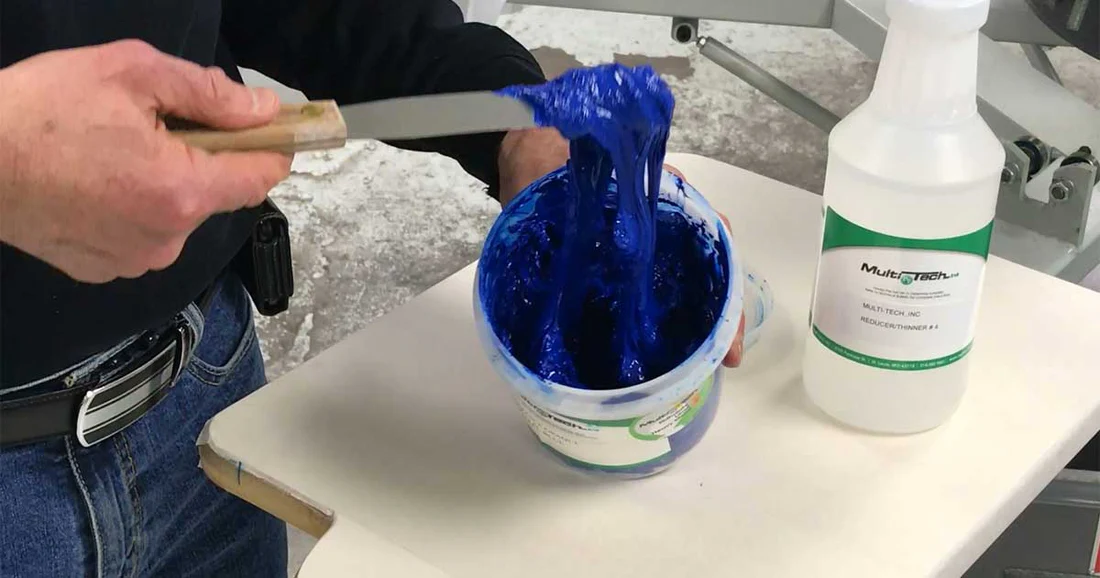
Types of Ink Thinners and Their Functions
Ink thinners come in a variety of types, each with different properties. Understanding these types and their respective roles will help ensure optimal results:
Organic Solvents
These are the most common type of ink thinners and are often used to reduce the viscosity of solvent-based inks.
- Alcohol-based thinners (Ethanol, Isopropyl Alcohol)
Function: Used in flexographic and gravure printing for fast evaporation and excellent flow. These thinners are particularly effective in inks that need rapid drying.
Key properties: Low boiling point, fast evaporation rate, good solvency for resins. - Aromatic Hydrocarbons (Toluene, Xylene)
Function: These thinners are used to adjust the viscosity of inks in flexographic and offset printing. They dissolve a wide range of resins and provide a longer drying time.
Key properties: High solvency power, moderate evaporation rate, suitable for high-performance inks. - Aliphatic Hydrocarbons (Mineral Spirits, Naphtha)
Function: Typically used in solvent-based ink systems where a milder thinning effect is required. These thinners have a lower evaporation rate and are used in formulations for flexible packaging or in environments with strict VOC regulations.
Key properties: Low toxicity, slow evaporation, moderate solvency power.

Ester-based Thinners
Ester thinners like ethyl acetate and butyl acetate are used in solvent-based inks for their excellent solvency properties.
- Function: These are used when inks need to dry at a moderate rate, offering a balance between drying time and printability. Commonly used in gravure and flexographic printing.
- Key properties: Excellent solvency for resins, good film-forming properties, moderate evaporation rate.
Ketone-based Thinners
Ketones, such as acetone and MEK (Methyl Ethyl Ketone), are fast-evaporating solvents typically used in inks for high-speed printing applications.
- Function: Ideal for fast-drying inks in screen and gravure printing, providing excellent solvency and reducing the ink’s viscosity. They can help with quick ink leveling and smooth surface coverage.
- Key properties: High volatility, fast evaporation, excellent solvency.
Water-based Thinners
For water-based inks, thinners are typically water or water + small amounts of co-solvents like ethylene glycol.
- Function: These thinners are used when the ink requires adjustment for print quality and drying time without increasing VOC emissions. Commonly used in flexographic and offset printing.
- Key properties: Low toxicity, eco-friendly, slower evaporation, ideal for sustainable printing practices.

Selection Criteria for Ink Thinners
Selecting the appropriate ink thinner depends on various factors, including the type of ink, the printing process, and the desired print outcome. Below are key factors to consider when choosing an ink thinner:
Type of Ink
Different types of inks require specific thinners:
- Solvent-based inks: Choose thinners with higher solvency power such as toluene, xylene, or ethyl acetate.
- Water-based inks: Water and mild co-solvents like propylene glycol are used to ensure proper flow without compromising the environmental profile.
- UV inks: UV inks usually do not require traditional thinners; however, if thinning is necessary, isopropyl alcohol or special UV-compatible thinners are used.
Printing Process
The thinner selected should align with the specific printing process:
- Flexographic Printing: Use alcohol-based or water-based thinners for high-speed printing and fast drying.
- Gravure Printing: Use ketones or aromatic hydrocarbon-based thinners for their moderate evaporation rates and excellent flow.
- Offset Printing: Aromatic hydrocarbons like toluene and isopropyl alcohol are common, though water-based thinners are gaining popularity for more sustainable printing.
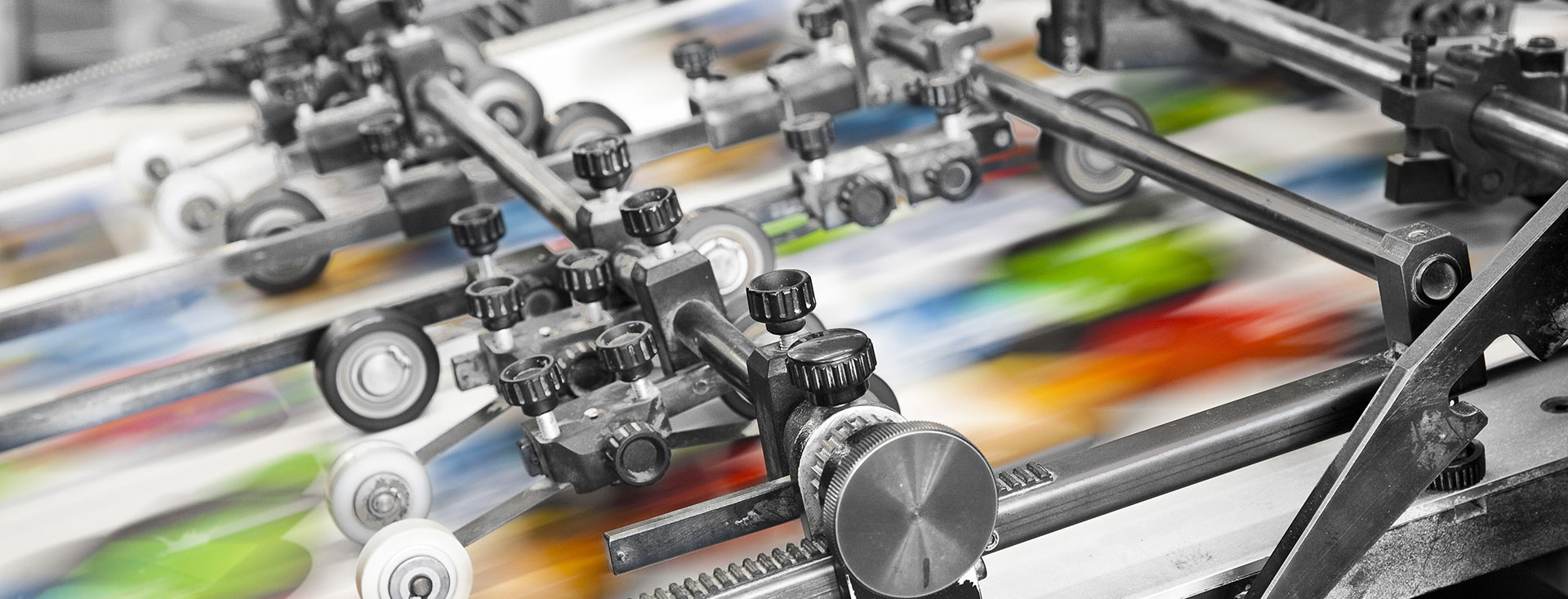
Substrate Type
The substrate being printed on influences the choice of thinner. For non-porous substrates like plastics or metals, thinners with lower surface tension and better wettability, such as acetone or toluene, may be preferred. For porous substrates like paper, water-based thinners are often sufficient.
Drying Time Requirements
- Fast drying: Use ketone-based thinners (acetone, MEK) or alcohols for applications where quick drying is critical (e.g., high-speed presses).
- Slow drying: Use aliphatic hydrocarbons or aromatic hydrocarbons to allow for longer working times.
Environmental and Health Considerations
If your operation prioritizes eco-friendly practices, choose thinners that are low in VOCs or water-based. This is especially important for compliance with environmental regulations such as EPA or EU VOC restrictions. Water-based thinners are preferred for their low toxicity and minimal environmental impact.
Best Practices for Using Ink Thinners
Mixing and Compatibility
- Always check compatibility: Ensure that the thinner is compatible with the ink and substrate. Some solvents may cause ink instability or adversely affect the print quality.
- Use the recommended thinner: Follow manufacturer guidelines for the correct type and amount of thinner to avoid compromising ink performance.
- Mix carefully: When adding thinners to the ink, do so gradually to avoid over-thinning. Mix thoroughly to ensure uniformity.
Proper Handling and Safety
- Ventilation: Always use ink thinners in a well-ventilated area to avoid inhalation of vapors. Follow local OSHA or EU guidelines for ventilation and air quality.
- Personal protective equipment (PPE): Wear appropriate PPE, including gloves, safety glasses, and respiratory protection, when handling thinners, particularly those that are hazardous or toxic.
- Storage: Store thinners in cool, dry places away from direct sunlight and open flames. Ensure containers are tightly sealed and labeled according to safety guidelines.
Waste Disposal
Dispose of excess thinners and used solvent containers according to local environmental regulations. Do not dispose of solvents down the drain or in regular waste streams. Use approved waste disposal methods, such as recycling or incineration.
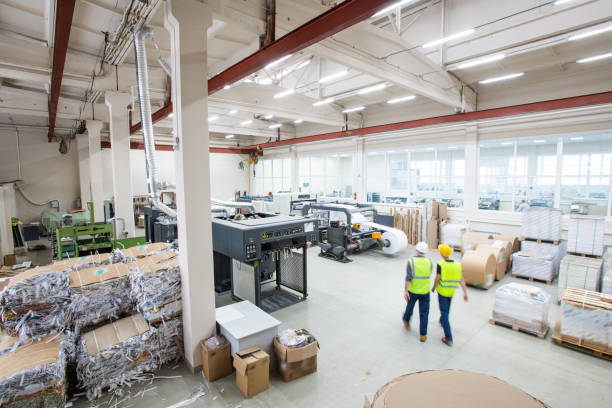
Troubleshooting
Too Viscous Ink
If the ink remains too thick even after adding the thinner, consider:
- Increasing the amount of thinner, but ensure it doesn’t negatively affect printability.
- Check the thinner’s compatibility with the ink and printing process.
Inconsistent Drying
If the ink takes too long to dry or dries too quickly:
- Slow drying: Consider using a thinner with a faster evaporation rate.
- Fast drying: Consider using a thinner with a slower evaporation rate to balance the drying time.
Poor Adhesion or Smearing
Inks with poor adhesion or smearing issues may require a different thinner to enhance flow or improve adhesion to the substrate. Try adjusting the thinning process or switch to a thinner that improves ink bonding properties.
Conclusion
Ink thinners are a vital component in printing ink formulations, offering precise control over ink viscosity, drying time, and print quality. Selecting the right thinner involves understanding the chemistry of both the ink and the substrate, as well as considering environmental, health, and safety factors. By following the guidelines provided here and adhering to best practices, you can ensure high-quality, consistent prints and optimize the overall printing process.
Contact K-Chem today for a free consultation and discover how our high-quality thinners can improve your manufacturing efficiency. Get in touch now to learn more and receive expert advice!
Thinners are an ideal solution for time saving and labor cost. With outstanding benefits and diverse applications, thinners will be a great choice for manufacturers that want to improve work efficiency.
K-Chem is one of the top thinner manufacturers in the Vietnam market. Located in Binh Duong province which is very convenient to deliver to packaging and paints manufacturers in the South East area.
K-CHEM VIETNAM CO., LTD
- N6B Road, Lot F, Phu Chanh 1 Industrial Park, Phu Chanh Ward, Tan Uyen City, Binh Duong Province, Vietnam
- Tel: +84 274 362 0218
- Email: info@k-chem.vn
- Website: https://k-chem.vn